Produkt | Zellenhalter für maßgeschneiderte Batterien |
Technologie | Bearbeitung, Vakuumguss, Schnellspritzguss |
Material | ABS, PUABS V0, PAGF30 |
Oberfläche | Durchgefärbt, Einfaches Polieren |
Zeitplan | 16 Tage/1. Bestellung, 26 Tage/2. Bestellung, 27 Tage/3. Bestellung |
Menge | 24 Teile für CNC, 90 Teile für Vakuumguss, 4000 Teile für Spritzguss |
Dies ist ein Beispiel für einen Kunden, der von Protolis bei jedem Schritt begleitet wurde, von der Prototypenentwicklung über die Kleinserienfertigung bis hin zur Massenproduktion. In jeder Phase wurden verschiedene Fertigungsmethoden eingesetzt, jede mit ihren eigenen Vorteilen und Herausforderungen.
Über unseren Kunden
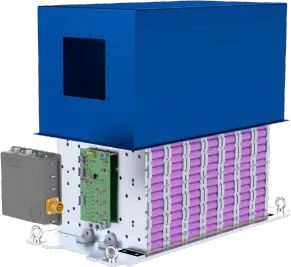
In Zusammenarbeit mit großen Industriekonzernen ist unser Kunde ein wichtiger Akteur im Bereich der Entwicklung innovativer Energielösungen. Er nutzt seine Expertise, um Energiespeichersysteme und maßgeschneiderte Batterien bereitzustellen, die den Anforderungen der anspruchsvollsten Sektoren wie Luft- und Raumfahrt sowie Automobilindustrie gerecht werden und gleichzeitig aktiv zur Energiewende beitragen.
Das Unternehmen ist stolz darauf, maßgeschneiderte Lösungen anzubieten, die auf die spezifischen Bedürfnisse seiner Kunden abgestimmt sind, mit einem Fokus auf Kleinserienproduktion. Durch diesen Ansatz erfüllt es die komplexesten Mobilitätsanforderungen und trägt gleichzeitig aktiv zur Transformation hin zu einer nachhaltigeren und elektrifizierten Wirtschaft bei.
Technische Herausforderungen und Lösungen
Abhängig von den verschiedenen Phasen des Projekts, von der Prototypenentwicklung bis hin zur Produktion, und den resultierenden Stückzahlen wurden verschiedene Fertigungsprozesse in Betracht gezogen.
Hier ist eine detaillierte Erklärung jeder Phase, zusammen mit den Herausforderungen und den Lösungen, die von Protolis bereitgestellt wurden:
Phase 1: Prototypenentwicklung
Die ersten 24 Stücke wurden mit CNC-Bearbeitung in ABS hergestellt, was Genauigkeit und Schnelligkeit bot, jedoch zu höheren Kosten.
Herausforderung und Lösung: Für kleine Stückzahlen (<= 25 Stück) wurde CNC-Bearbeitung aufgrund ihrer Geschwindigkeit und hohen Präzision trotz höherer Kosten bevorzugt.
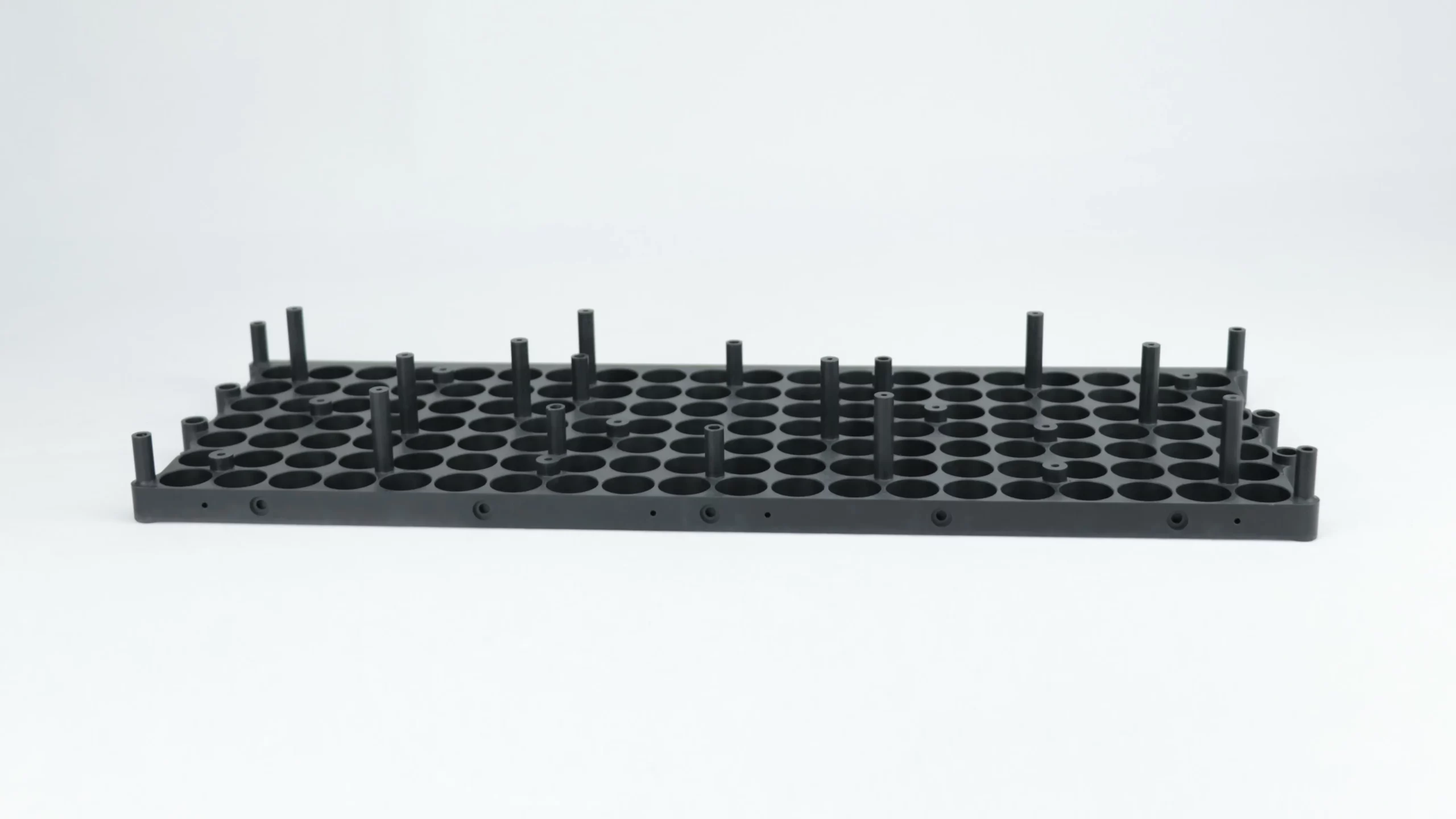
Phase 2: Kleinserienfertigung
Für die folgenden 90 Stücke haben wir die Vakuumgussfertigungstechnologie eingesetzt.
Herausforderungen: Vakuumguss erwies sich als die komplexeste Phase, um Ebenheit und Toleranzen zu erfüllen.
Lösungen: Es wurden Maßnahmen ergriffen, um die Ebenheit und Toleranzen der 234 Löcher während des Vakuumgussprozesses zu kontrollieren. Der Einsatz von Vorrichtungen half, Deformationen entgegenzuwirken. Funktionsprüfvorrichtungen und andere zur Anpassung von Deformationen wurden erstellt. Strenge Nachkontrollen wurden durchgeführt, um die Maßtoleranzen sicherzustellen, trotz möglicher Abweichungen in den Abmessungen der Rippen.
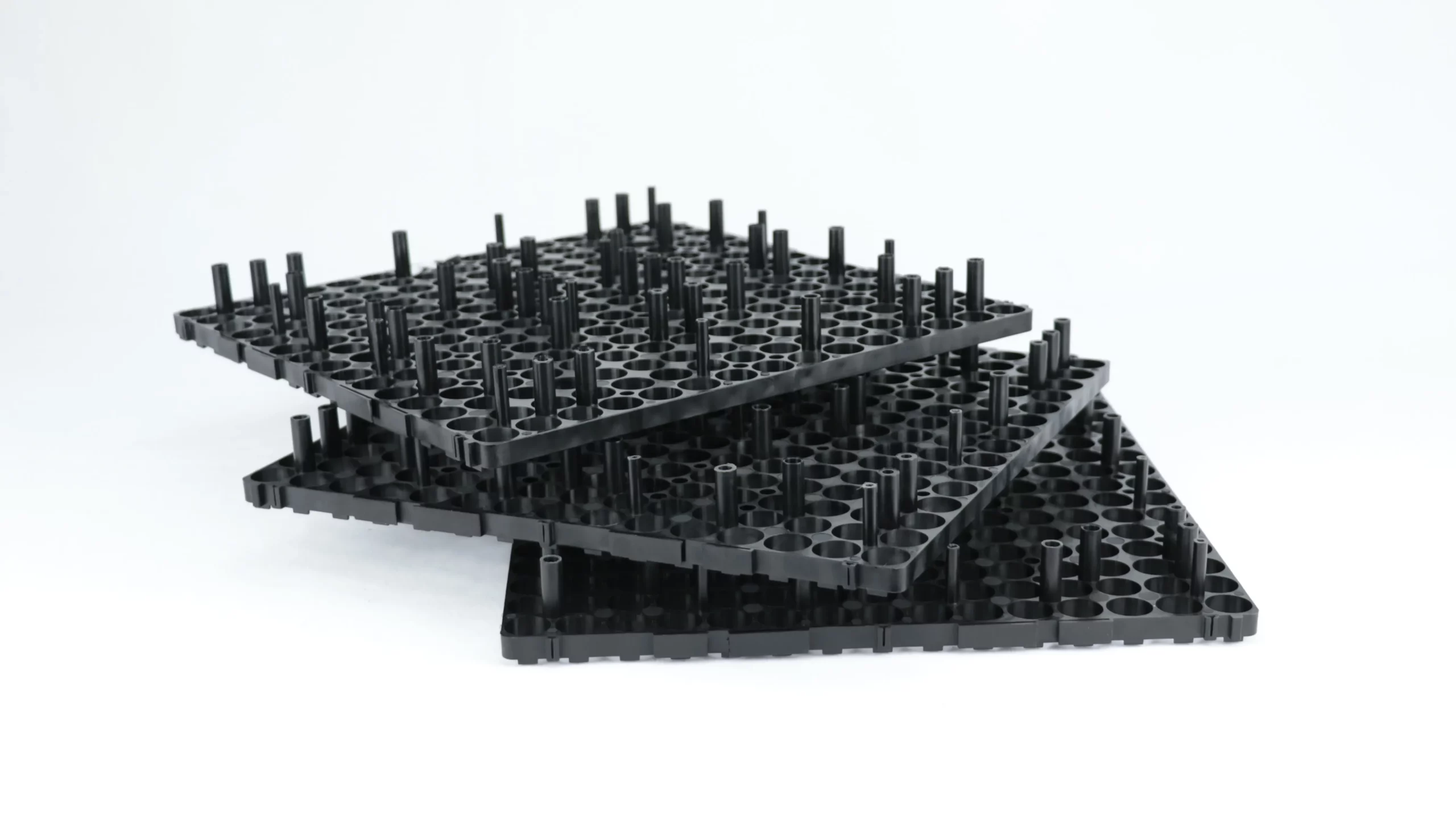
Phase 3: Massenproduktion
Für die Endproduktion von 4000 Stück war der Übergang zum Schnell-Spritzguss entscheidend, um die Produktion zu skalieren und gleichzeitig die Kostenwettbewerbsfähigkeit zu gewährleisten.
Herausforderung: Anfangsinvestitionen sind erforderlich, aber sie machen sich bezahlt, da die Stückkosten mit steigender Produktionsmenge sinken.
Lösungen: Der Wechsel zum Kunststoffspritzguss bietet Präzision in Industriequalität und minimiert Deformationen. Zusätzlich hat sich die Einhaltung der Toleranzen erheblich verbessert.

Ergebnisse
Der Übergang von einer Technologie zur anderen ermöglichte eine gesteigerte Produktion bei kontrollierten Kosten, stabiler Qualität, verringerten Deformationen und gleichzeitig der Aufrechterhaltung zufriedenstellender Toleranzen.
Der Übergang von CNC zu Vakuumguss führte zu einer Reduzierung der Produktionskosten um 60%. Der Wechsel vom Vakuumguss zum Spritzguss erzielte eine Reduzierung der Produktionskosten um mehr als 90%, insbesondere nach Abdeckung der anfänglichen Werkzeugkosten für den Spritzguss.
- Erfolgreiche Skalierung der Produktion von 24 Stück auf 4.000 Stück.
- Kostenwirksamkeit durch den Einsatz unterschiedlicher Fertigungsprozesse in verschiedenen Phasen gesteuert.
- Gewünschte Präzision erreicht und Deformationen durch Vorbereitung, sorgfältige Planung und Kontrollmaßnahmen minimiert.
- Unseren Kunden durch verschiedene Fertigungsherausforderungen geführt.
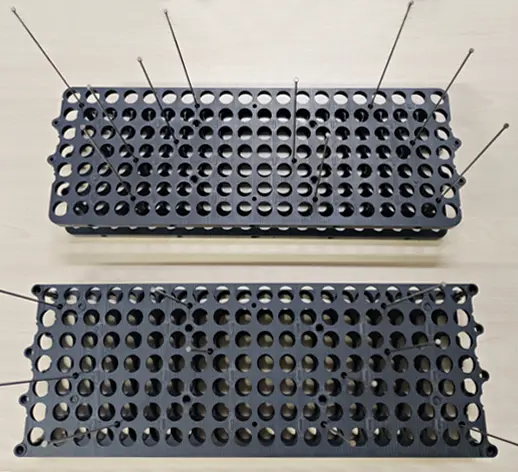