Introduction
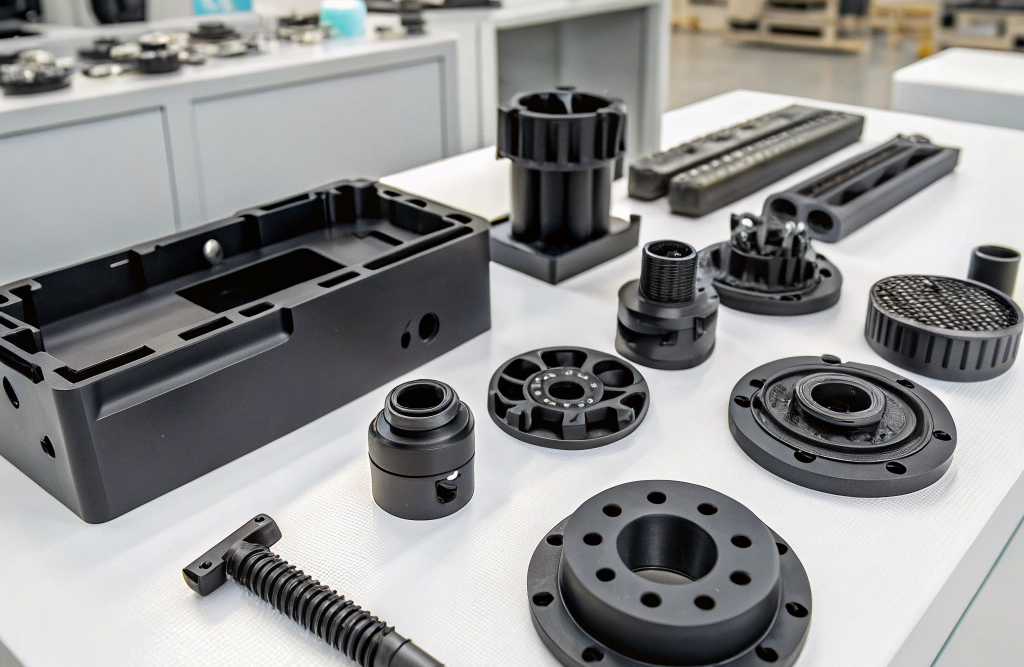
Rapid prototyping is a crucial step in any industrial project. It enables validation of a concept, identification of necessary improvements, and modifications before mass production.
The primary goal of rapid prototyping is to reduce risks and costs by detecting potential issues and gathering user feedback early in the development process. This allows for quick iterations and refinements before finalizing the product.
While 3D printing is often the go-to technology due to its speed, flexibility, and ease of use, CNC (Computer Numerical Control) machining is a popular alternative for rapid prototyping. CNC machining offers a level of precision and material versatility that 3D printing cannot always match. Let’s explore in detail why CNC machining is an excellent choice for rapid prototyping.
Traditional prototyping technologies
Historically, rapid prototyping technologies were dominated by methods such as prototype molding, low-pressure casting, and 3D printing. 3D printing has revolutionized prototyping by allowing the direct creation of parts from digital models. Thanks to its speed, low startup cost, and flexibility, it has become one of the most popular methods.
However, 3D printing has limitations, particularly regarding material selection and mechanical strength. For example, while plastic materials like ABS and PLA are widely used in 3D printing, they are not always suitable for applications requiring more durable or precise components. Additionally, 3D-printed parts may lack the smooth finish or structural integrity of machined parts.
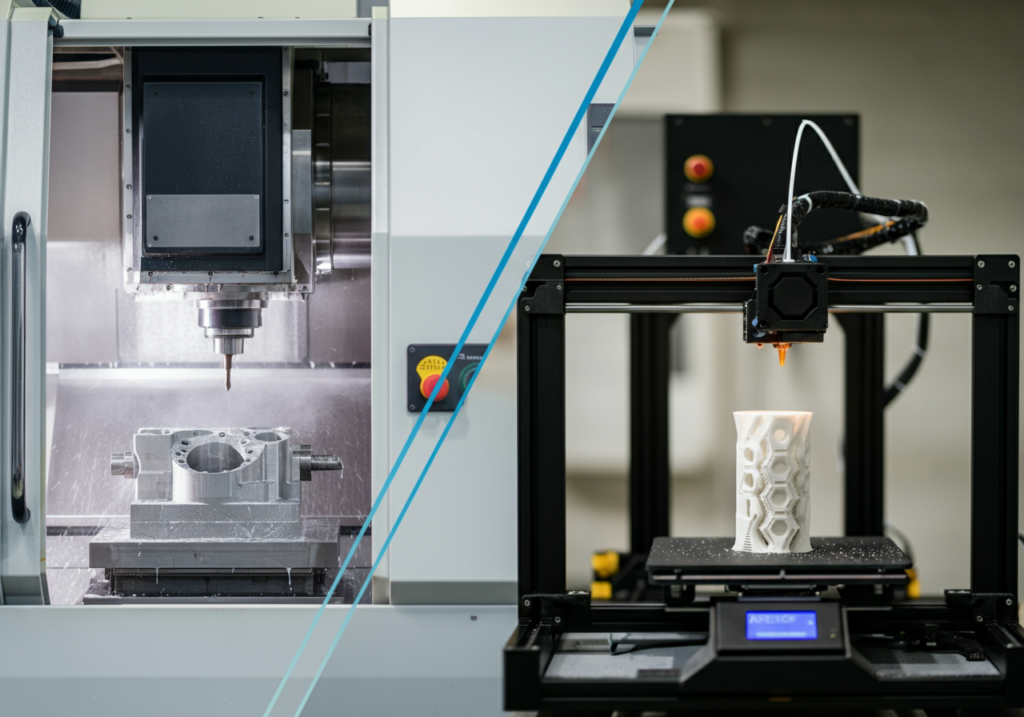
CNC machining, on the other hand, is a subtractive manufacturing technique that removes material from a solid block to create parts. This allows for the use of a wide range of materials, including metals, engineering plastics, and specialized alloys, providing greater variety and durability in prototyping.
What is CNC machining?
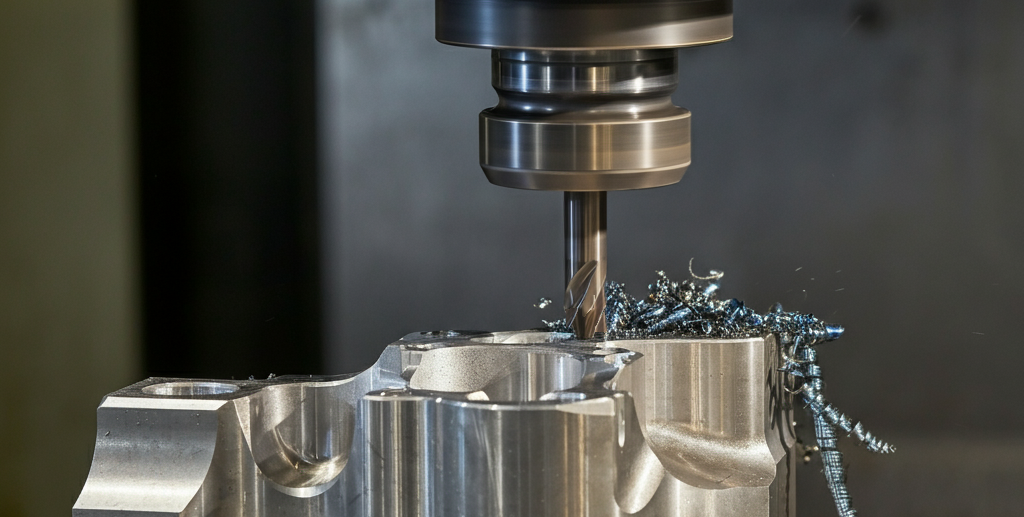
CNC machining is a subtractive manufacturing process that uses computer-controlled machines to cut, mill, or turn materials into precise components. Unlike 3D printing, which builds objects layer by layer, CNC machining removes material from a solid block based on digital design instructions (typically CAD files). This highly automated process ensures exceptional precision and repeatability.
There are several types of CNC machining, each suited for specific applications:
CNC milling
CNC milling is one of the most common machining methods. It involves using a rotating cutter to remove material from a solid block. CNC milling is ideal for manufacturing complex parts and irregular geometries. Thanks to its precision and the flexibility of cutting tools, it is widely used for applications ranging from mechanical parts to electronic components.
CNC turning
CNC turning is used to machine cylindrical or conical parts. This process involves rotating the workpiece while a cutting tool moves along its surface. CNC turning is particularly useful for producing shafts, tubes, and supports with smooth and precise surfaces. These machines can also perform complex operations such as threading and drilling with high accuracy.
5-Axis CNC machining
5-axis CNC machining is an advanced technique that allows machining on five axes simultaneously, offering great flexibility in creating complex geometries. This enables the production of sophisticated components in a single operation, reducing manufacturing steps and improving overall precision. 5-axis machining is commonly used in high-precision industries such as aerospace, automotive, and high-performance tooling.
CNC machining has evolved with technological advancements, making machines more accessible and easier to use, even for small-scale production or prototyping.
New generations of CNC machines have simplified their operation, making this technology more accessible and efficient for rapid prototyping.
Advantages of CNC machining for rapid prototyping
1. CNC machining is fast
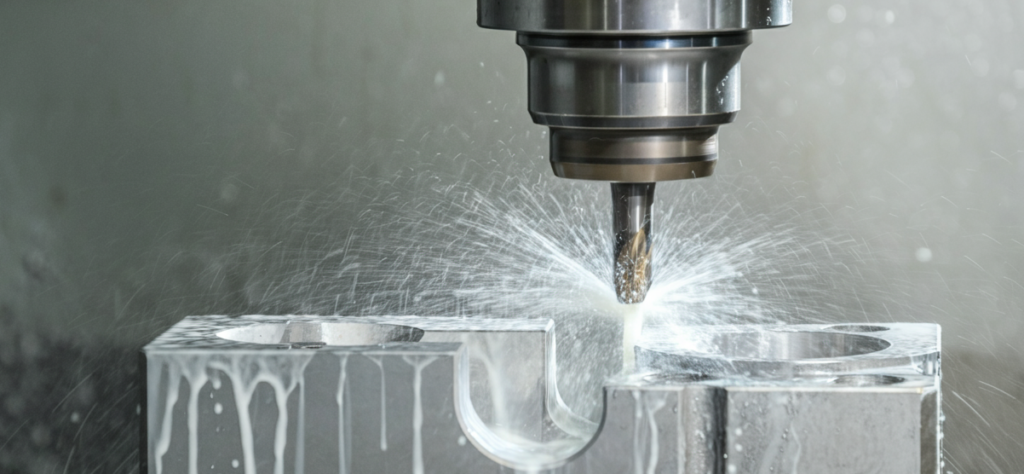
One of the primary advantages of CNC machining for rapid prototyping is its speed. Unlike some molding techniques that require expensive and time-consuming mold fabrication, CNC machining can produce a prototype in just a few hours. This is particularly beneficial for accelerating product development and enabling quick design iterations.
2. No expansive tooling required with CNC machining
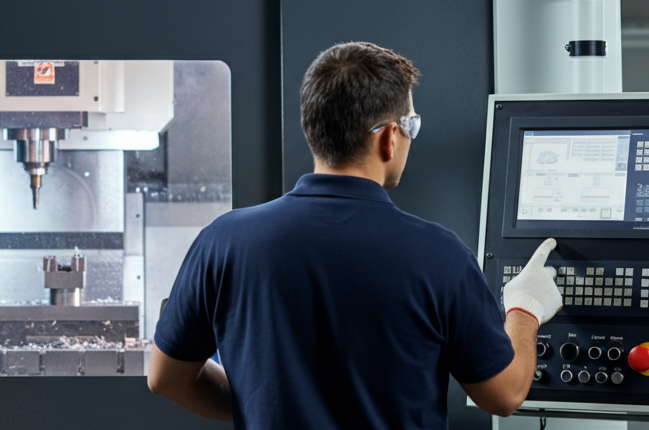
CNC machining stands out from other manufacturing methods, such as injection molding or sand casting, because it does not require molds or specialized tooling. By simply using a digital CAD file, CNC machines can directly manufacture parts from raw materials. This significantly reduces production costs and lead times, making it especially advantageous in the early stages of product development.
3. CNC machining delivers high precision
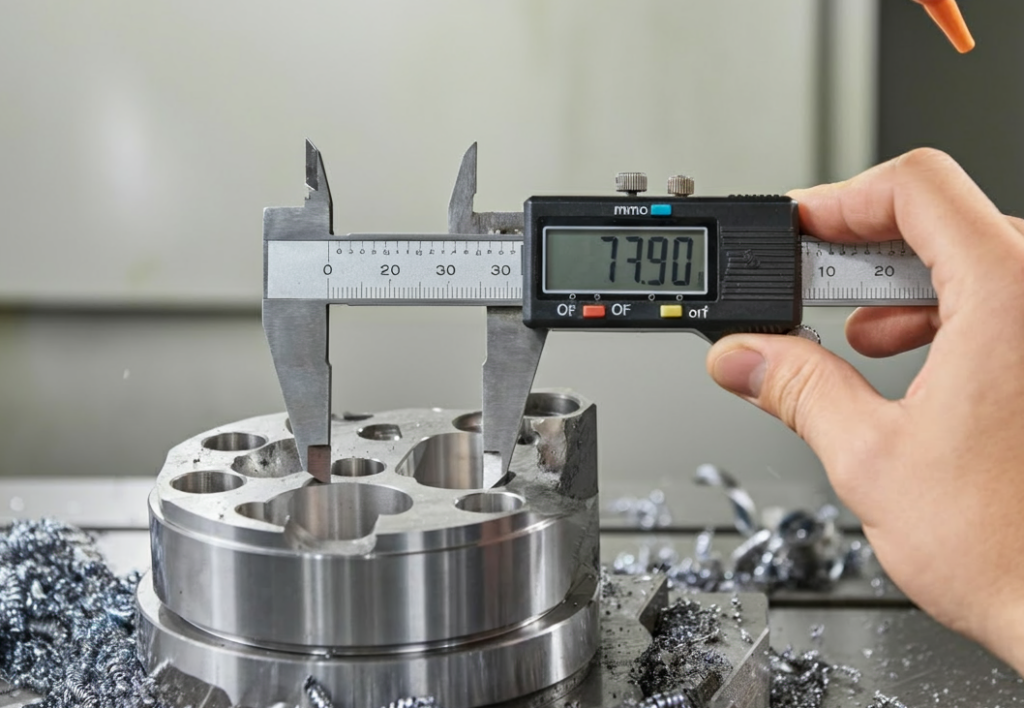
CNC machining delivers exceptional precision, with tolerances as tight as ±0.01 mm (or 0.0004 inches). This level of accuracy is crucial for industries where part performance and prototype quality are essential. Unlike 3D printing, where layer-by-layer construction can result in imperfections, CNC machining ensures flawless surface finishes and exact dimensions. This is particularly important for aerospace, automotive, and medical device manufacturing.
To learn more about CNC machining precision and how it can enhance your prototypes, contact us.
4. Quick iterations and modifications with CNC prototyping

Digital files used for CNC machining can be quickly adjusted, allowing for fast modifications and regular iterations to refine prototypes. When changes are needed, simply updating the CAD model enables rapid production of new prototypes without restarting the entire manufacturing process. This flexibility allows engineers and designers to test new ideas quickly, reducing the time between prototype versions.
5. CNC machining supports a wide range of materials
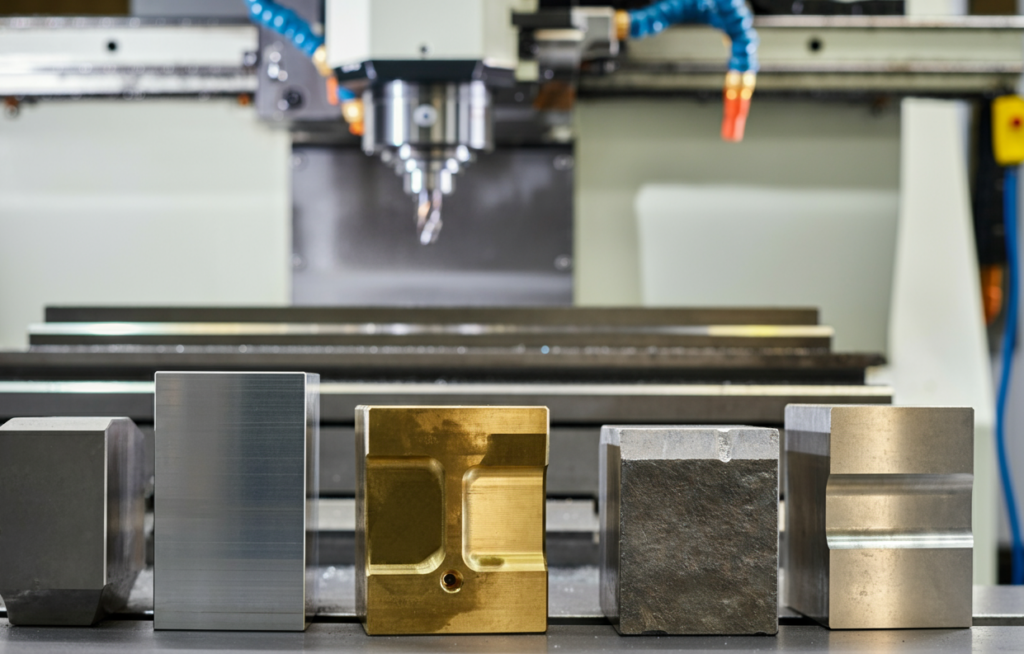
CNC machining offers the advantage of working with a vast selection of materials, including metals such as aluminum, titanium, and stainless steel, as well as engineering plastics like PEEK, ABS, and PMMA. These materials are often necessary for applications requiring strength, durability, and high performance. In contrast, 3D printing is limited to materials like plastic and resin, which are not always suitable for industrial applications.
Limitations of CNC machining
- Higher Cost for Certain Parts: For highly complex parts in large quantities, CNC machining can be more expensive than other methods like injection molding. Additionally, costs may increase for very small components or those requiring specific surface finishes.
- Geometric Limitations: While 5-axis machining has expanded possibilities, certain highly complex geometries—especially those requiring multiple setups or special orientations—can still be challenging to machine efficiently.
How Protolis can support your rapid prototyping needs
At Protolis, we offer comprehensive CNC machining solutions for rapid prototyping:
- Material selection: A wide range of materials tailored to your project, from engineering polymers to specialized metal alloys.
- Finishing options: Various surface treatments (polishing, anodizing, painting) for both functional and aesthetic requirements.
- Technical support: Guidance on design and optimization for your prototypes.
Contact us to explore our services and accelerate your innovation with Protolis!