Product | Fluid connection components |
Technology | Injection molding |
Material | PA66GF35 |
Finish | Machine polishing |
Timeline | 42 days |
Quantity | 80 sets |
Protolis was tasked with manufacturing plastic injection molded prototype parts and assembling these parts to verify their pressure resistance. The goal was to ensure a perfect fit between the two parts to guarantee the proper functioning of the fluid connector.
This project involved the use of a prototype mold, as well as the implementation of precise dimensional controls to ensure the integrity and functionality of the final component.
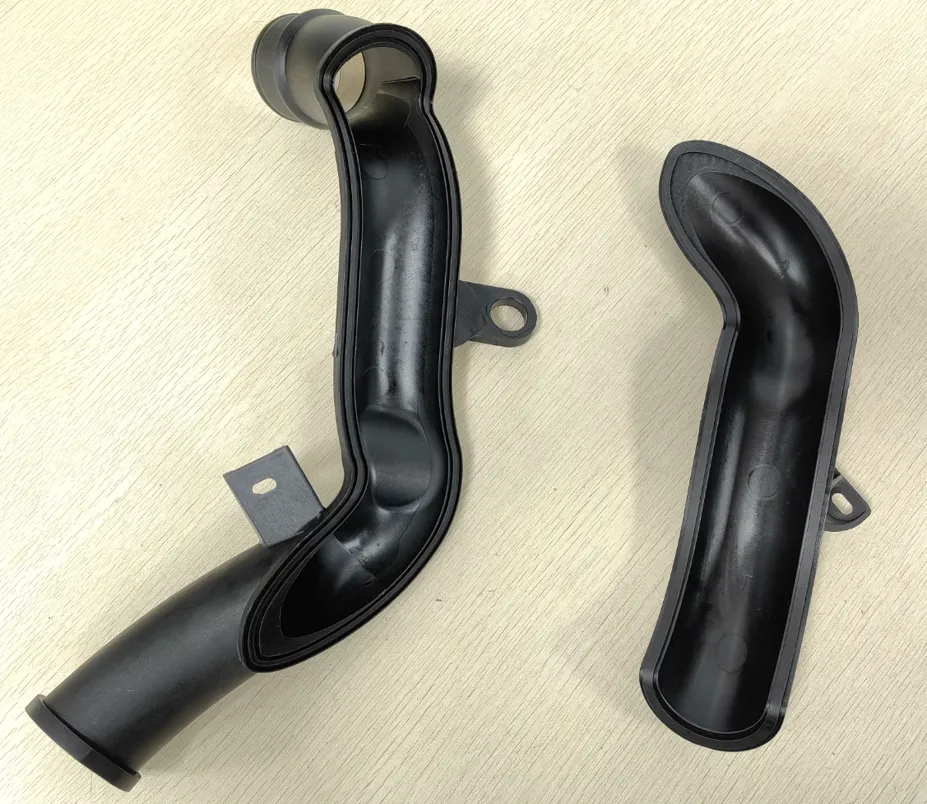
About our client
Our customer is a recognized expert in mold design and manufacturing, as well as in the production of plastic parts in small and medium series, using injection molding and extrusion-blow molding techniques.
Technological challenges
1. Complex mold movements
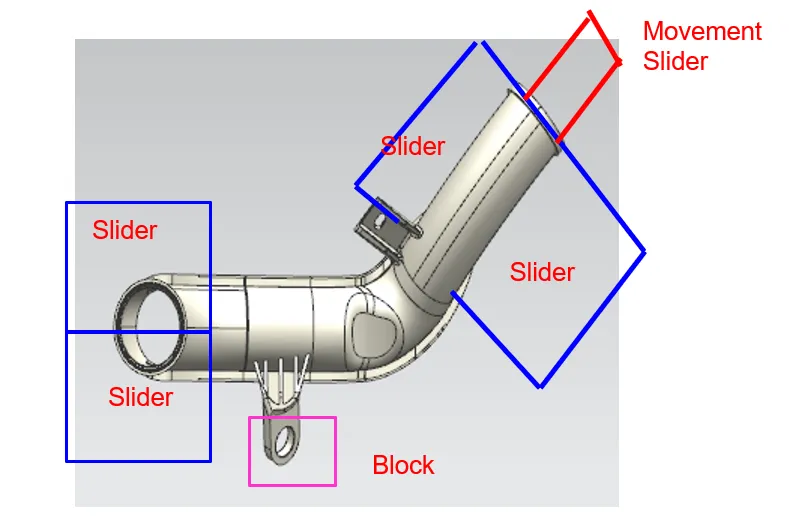
The prototype mold used for this project featured multiple movements (six in total), some of which were manual, allowing for cost reduction during the prototyping phase. This complexity required special attention to allow for the demolding of all shapes.
2. Real-world condition testing
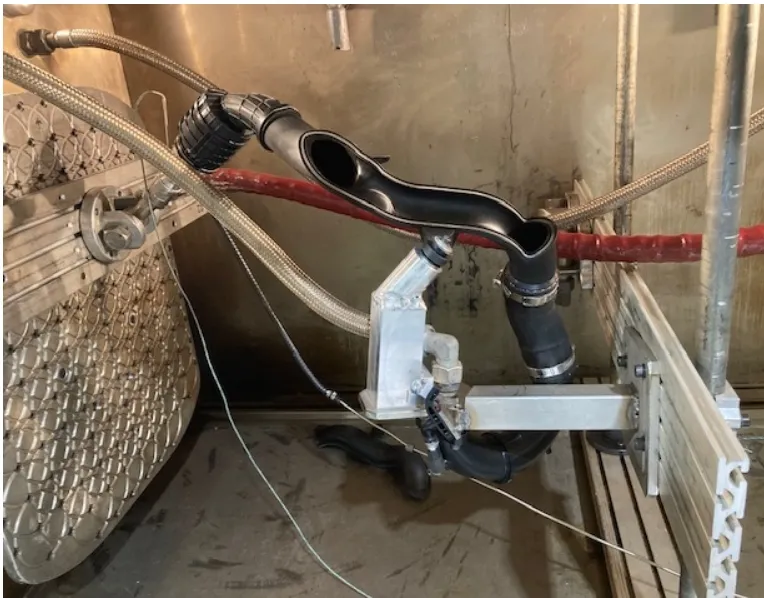
After assembly, the component was mounted on a machine for testing under real-world conditions, as shown in the photo. This step was crucial to validate the performance of the component under actual working conditions.
3. Insertion of the stainless steel ring
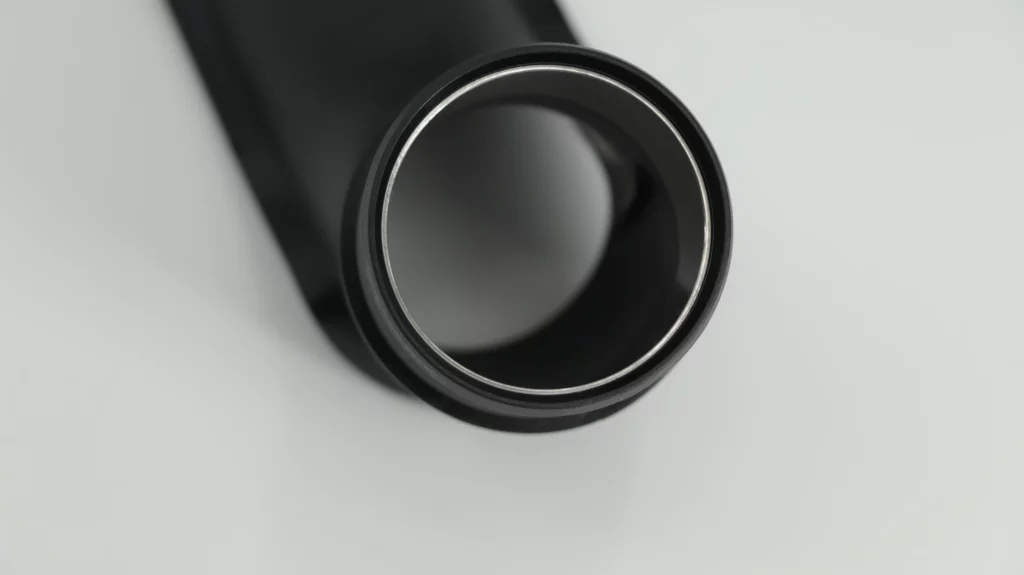
A stainless steel ring was added after molding. Its diameter had to be precise to ensure a perfect press-fit assembly. This precision was critical to guarantee the sealing and durability of the fluid connection.
4. Dimensional control and deformation prevention
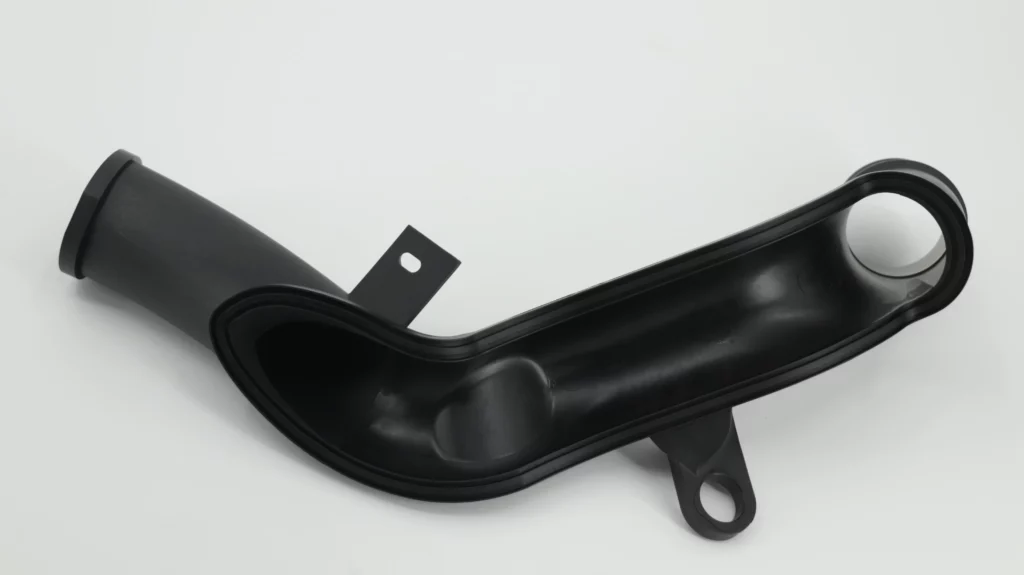
To prevent any deformation of the component, several measures were implemented:
- Plastic injection parameters: the injection molding parameters were carefully adjusted to avoid any distortion.
- Mold cooling: the mold cooling process was optimized to minimize the risk of thermal deformation.
- Inspection fixtures: custom inspection fixtures were produced to verify the dimensions of the component after molding and ensure its compliance.
Result
Through meticulous management of the production process and the use of appropriate prototype tooling, we successfully assembled and tested the fluid connection component.
Precise controls over plastic injection, mold cooling, and real-world condition testing ensured pressure retention and optimal performance of the part. The use of ultrasonic welding for attaching the upper component provided a reliable and durable bond.
The project was a success, delivering a fully functional prototype duct component, ready for real-world testing.
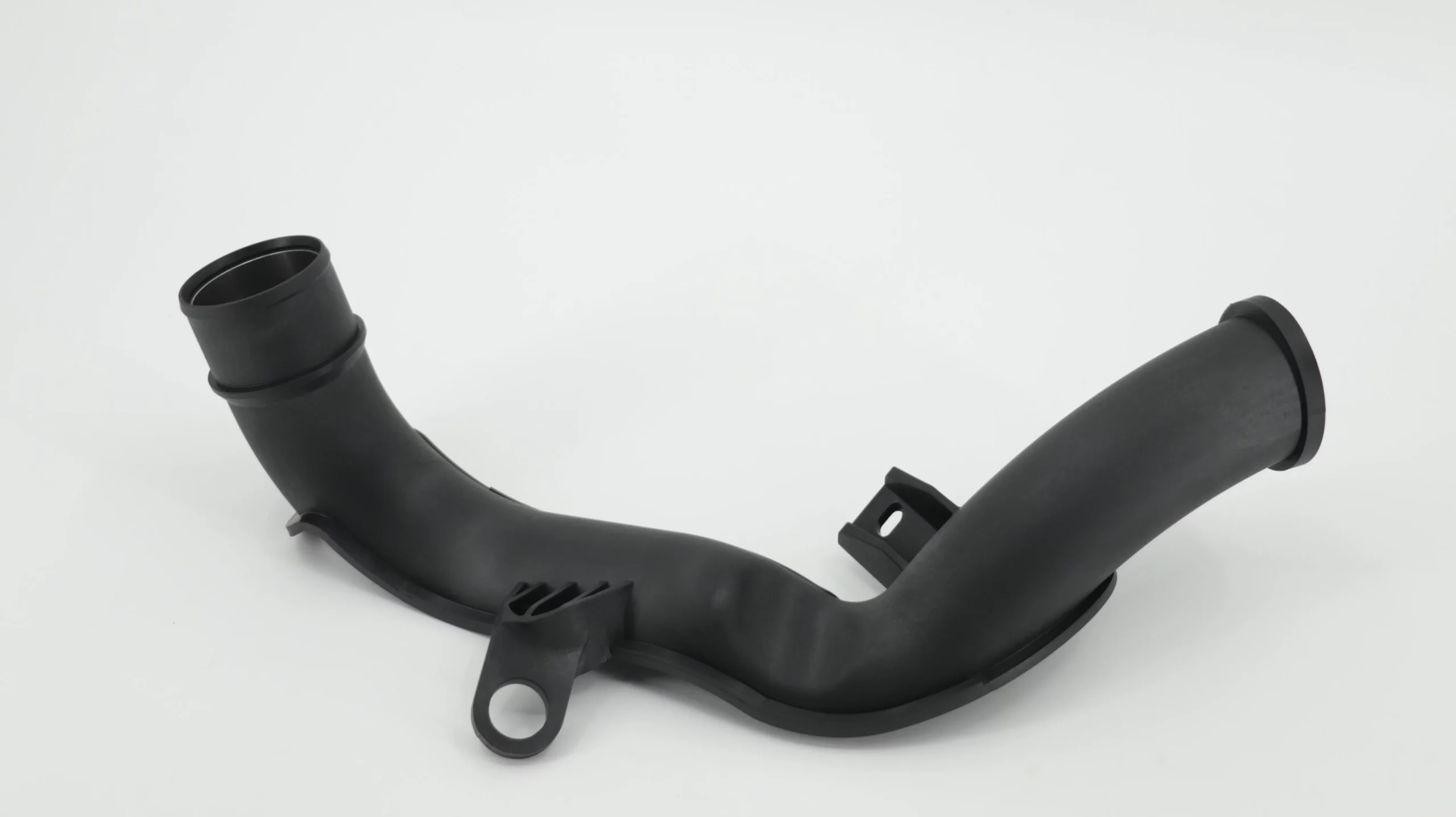